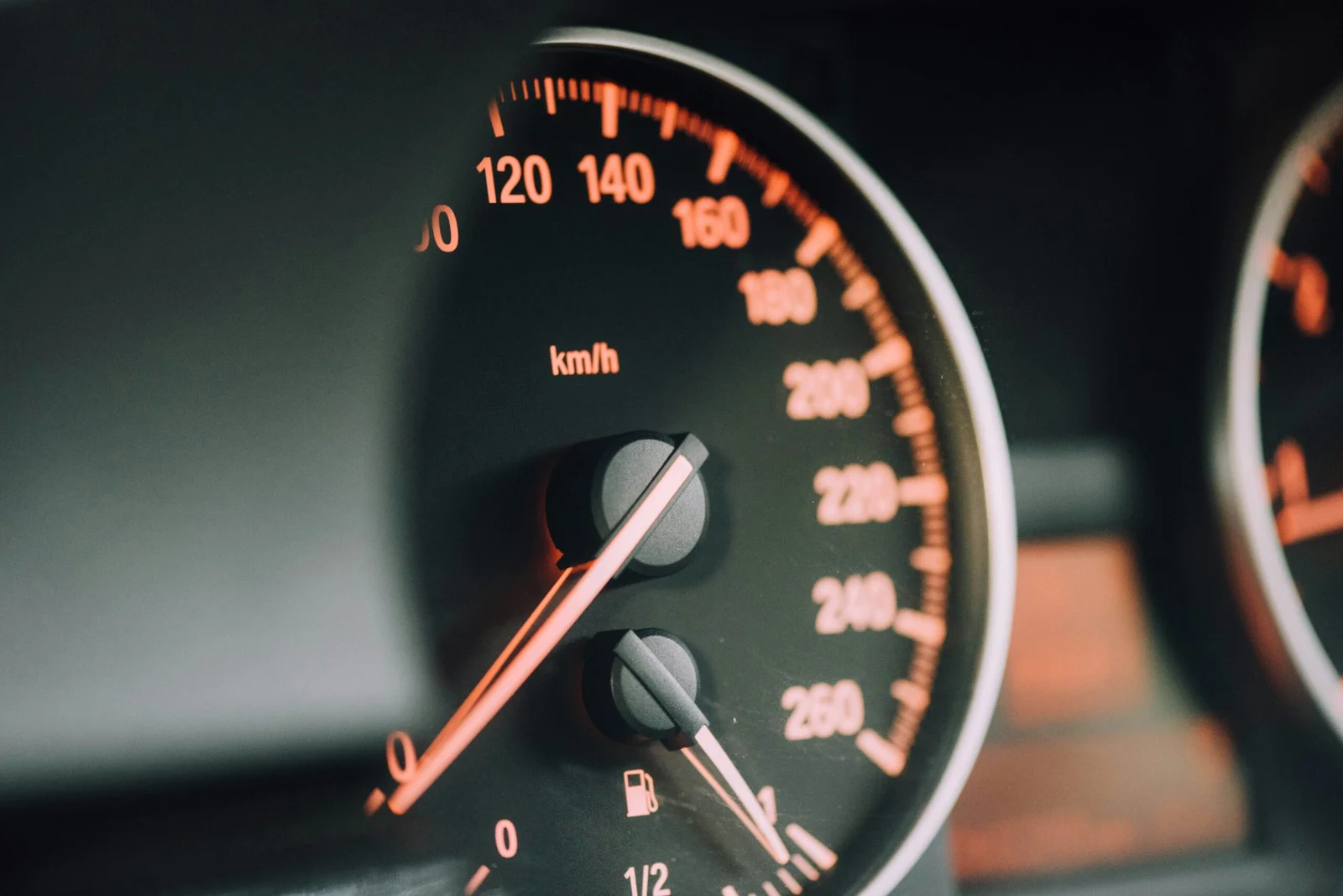
The Role of Robotics in Car Manufacturing
Introduction to Robotics in Manufacturing
The integration of robotics in the manufacturing sector has significantly transformed various industries, with the automotive industry being a primary beneficiary of these technological advancements. The journey of robotics began in the mid-20th century when the first industrial robots were introduced to automate repetitive tasks, improving efficiency and productivity. The introduction of these machines allowed manufacturers to streamline operations and reduce labor costs while enhancing precision and consistency in production processes.
In the 1960s, significant milestones were achieved, such as the creation of Unimate, the first robotic arm used in a General Motors plant. This pioneering development marked the beginning of a new era in car manufacturing, where automated systems started taking on skilled labor roles traditionally performed by humans. As technology progressed through subsequent decades, robotics saw advancements in artificial intelligence, machine learning, and sensor technologies, which paved the way for more sophisticated robotic systems capable of performing complex tasks.
The 1980s witnessed a surge in robot adoption within automotive manufacturing as companies sought to improve safety and efficiency. With the advent of computer numerical control (CNC) machines, robots became more versatile, allowing for greater integration into the production line. During this period, innovative entities began to explore collaborative robots, or cobots, designed to work alongside human operators, enhancing the synergy between automation and human labor in car factories.
By the 2000s, the widespread adoption of robotics in the automotive sector led to significant improvements in quality control and manufacturing flexibility. Robots were not only employed in assembly lines but also in welding, painting, and even logistics. This evolution underscored the critical role that robotics would play in shaping the future of automotive manufacturing, establishing a foundation for ongoing innovation in the industry. Today, the advancement of robotics continues to redefine the parameters of manufacturing, setting the stage for an increasingly automated future.
Types of Robotics Used in Car Manufacturing
The automotive manufacturing industry employs several types of robotics to enhance productivity, precision, and safety. Among these, industrial robots stand out as the most widely utilized. These robots are typically large and powerful, designed for tasks such as welding, painting, and assembly. Their ability to work at high speeds while maintaining consistent accuracy makes them invaluable in mass production environments. Industrial robots are usually programmed to perform specific functions, adapting to various tasks throughout the vehicle production process.
Collaborative robots, commonly known as cobots, represent another significant category of robotics in the automotive sector. Unlike traditional industrial robots, cobots are designed to work alongside human workers safely. They are typically smaller, more flexible, and equipped with advanced sensors that allow them to detect human presence. This enables them to assist with tasks that require a human touch, such as quality inspections or delicate assembly processes. The integration of cobots not only improves efficiency but also enhances working conditions, allowing human workers to focus on more complex and cognitively demanding responsibilities.
Another emerging type of robotics in car manufacturing is autonomous mobile robots (AMRs). These robots are equipped with advanced navigation capabilities, allowing them to move materials and components throughout the manufacturing floor without the need for human intervention. By utilizing AMRs, manufacturers can streamline their supply chain and enhance material handling efficiency. AMRs can transport parts from one station to another or bring tools to workers, thereby reducing downtime and optimizing workflow.
In summary, the application of different types of robotics—industrial robots, collaborative robots, and autonomous mobile robots—plays a crucial role in modern car manufacturing. Together, these robotic systems enhance productivity and flexibility, allowing manufacturers to meet the increasing demands of the automotive market more effectively.
Benefits of Robotics in Car Manufacturing
The incorporation of robotics into car manufacturing has ushered in a new era of efficiency and precision, significantly transforming production processes. One of the most notable advantages is the increased precision that robotics offers. Machines equipped with advanced sensors and AI can execute highly intricate tasks with a level of accuracy that surpasses human capabilities. This precision is crucial in car manufacturing, where minute errors can lead to performance issues or safety hazards. By minimizing these errors, manufacturers can assure higher quality standards in their vehicles.
Furthermore, robotics contribute to enhanced productivity. Automated systems can operate continuously, functioning day and night without the breaks that human workers require. This capability allows for a significant increase in output, enabling factories to meet growing consumer demands effectively. For instance, companies like Tesla have employed robotic assembly lines that have dramatically increased their production rates while maintaining quality.
Safety within the manufacturing environment is another area where robotics excels. By taking over hazardous tasks, such as metal cutting and handling heavy components, robots reduce the risk of workplace injuries. This shift not only protects workers but also leads to lower insurance costs and reduced liability for manufacturers. The implementation of robotics has proven to enhance overall workforce safety, creating a more secure working environment.
Cost efficiency is yet another critical benefit. Although the initial investment in robotic technology can be substantial, the long-term savings associated with decreased labor costs, reduced waste, and increased operational efficiency often outweigh these costs. For instance, companies have reported substantial reductions in manufacturing costs per vehicle after integrating robotic systems. As the automotive industry continues to innovate, it is evident that the role of robotics is pivotal in driving these benefits, making them essential for modern car manufacturing.
Challenges and Limitations of Robotics in Car Manufacturing
The integration of robotics into car manufacturing has revolutionized production processes, but it is not without its challenges and limitations. One of the primary obstacles faced by manufacturers is the high initial investment costs associated with acquiring robotic systems. The price of advanced robots, along with the necessary infrastructure modifications, can be prohibitively expensive for many companies, particularly smaller manufacturers. This financial barrier can hinder widespread adoption and limit the potential benefits that robotics can offer in terms of productivity and efficiency.
Moreover, the complexity of robotics necessitates a workforce that is not only skilled in operating these machines but also proficient in their maintenance and programming. As factories increasingly adopt automated technologies, the demand for skilled workers in robotics and related fields has surged. This shift requires investment in training programs to equip existing employees with the necessary skills. Manufacturers may find it challenging to recruit individuals who possess both technical expertise and familiarity with robotic systems, leading to a potential skills gap in the industry.
Another significant concern is the potential for job displacement caused by automation. As robots take over repetitive tasks, there is a growing apprehension among the workforce about job security. While robotics can enhance efficiency and lower production costs, the social implications of reduced job opportunities must be addressed through thoughtful workforce transition strategies. Consequently, manufacturers must balance the advantages of robotics with strategies that mitigate negative impacts on employment, fostering a collaborative environment where humans and robots can coexist effectively.
In summary, while the advantages of robotics in car manufacturing are substantial, companies must navigate several challenges, including high costs, the need for skilled labor, and the potential displacement of jobs. Addressing these challenges is crucial for the sustainable integration of robotic systems in the automotive industry.
The Future of Robotics in Car Manufacturing
The automotive industry is on the cusp of significant transformation, largely driven by the advancements in robotics. As manufacturers strive for increased efficiency and precision, the integration of artificial intelligence (AI) and machine learning into robotic systems has become imperative. These technologies enable robots to learn from their environment, enhance their decision-making capabilities, and improve the overall manufacturing process. As a result, we can expect to see more intelligent robots that adapt to various tasks, optimizing production lines to adapt to changing requirements seamlessly.
Furthermore, the rise of the Internet of Things (IoT) is enhancing the capabilities of robotics in car manufacturing. IoT devices facilitate real-time communication between machines, allowing robots to share data with human operators and other equipment within the manufacturing ecosystem. This connectivity leads to increased operational transparency, enabling manufacturers to optimize workflows and reduce downtime caused by equipment malfunctions. By collecting and analyzing data from multiple sources, manufacturers can now forecast issues before they arise, further enhancing efficiency and reliability in the production process.
Another emerging trend is the greater incorporation of collaborative robots, or cobots, within the automotive industry. Unlike traditional robots that operate independently, cobots are designed to work alongside human workers, augmenting their capabilities and enhancing productivity. This collaboration fosters a safer working environment, allowing for a harmonious balance between human expertise and robotic efficiency. As the automotive landscape continues to evolve, the symbiotic relationship between humans and machines will be pivotal in meeting the demands of the market.
In conclusion, the future of robotics in car manufacturing will be characterized by sophisticated AI, enhanced data connectivity through IoT, and collaborative efforts between humans and robots. These developments promise to shape a more efficient, responsive, and innovative automotive manufacturing sector.
Case Studies: Successful Implementation of Robotics
The automotive industry has undergone significant transformations due to the integration of robotics into manufacturing processes. A notable example is Ford Motor Company, which implemented robotics in its assembly line to improve efficiency and accuracy. Faced with high demand and competition, Ford adopted robotic technology to automate repetitive tasks, such as welding and painting. This transition not only enhanced production speed but also reduced human error, resulting in higher quality vehicles and improved safety for assembly line workers.
Another remarkable case is that of General Motors (GM), which faced challenges related to labor costs and production inefficiencies. In response, GM invested in advanced robotic systems equipped with artificial intelligence (AI) capabilities. The robots were programmed to collaborate closely with human workers, facilitating a flexible production environment that could adapt to varying model demands. The successful integration led to a notable 20% increase in production efficiency and a significant reduction in accidents on the floor, highlighting the balance between robotics and workforce safety.
Toyota also stands out with its implementation of robotics within the Toyota Production System. Initially, the company encountered bottlenecks in component assembly, which hampered the overall production timeline. By introducing collaborative robots (cobots), Toyota was able to streamline its processes, allowing humans and machines to work side by side effectively. The result of this melding of capabilities was a smoother workflow that cut assembly times by 15% and boosted overall productivity. These examples highlight the critical role robotics play in enhancing automotive manufacturing, addressing challenges, and optimizing productivity.
Robotics and Sustainability in Car Manufacturing
The integration of robotics in car manufacturing is pivotal in advancing sustainability initiatives within the automotive industry. One of the primary benefits of employing robotic systems is waste reduction. Automated processes minimize human error, which often leads to material waste during production. By ensuring a precise and consistent manufacturing output, robots contribute to the effective utilization of resources, leading to reduced scrap rates and more efficient material management.
Moreover, robotics significantly enhance energy efficiency in manufacturing processes. Robots can operate optimally at high speeds and with precise control, thereby reducing energy consumption compared to traditional manufacturing methods. For instance, advanced robotic arms can execute tasks such as welding and painting with minimal energy expenditure. This not only lowers the carbon footprint of the production facility but also allows manufacturers to harness innovative technologies, such as regenerative energy systems, to further decrease energy usage and promote renewable energy within their production lines.
Another critical aspect where robotics supports sustainability is through its role in the production of electric and hybrid vehicles. As the automotive industry shifts towards greener alternatives, robotics facilitates the complex assembly processes required for these advanced vehicles. Robots are adept at handling the integration of electric drivetrains and batteries, components that require specialized knowledge and precision. Additionally, the ability of robots to perform complex tasks in a controlled manner paves the way for improved safety standards and alignment with environmental regulations.
Committed to fostering sustainability, car manufacturers are increasingly recognizing the strategic value of robotics in achieving their environmental goals. The combination of waste reduction, energy efficiency, and enhanced capabilities for producing electric vehicles forms a robust foundation for a more sustainable future in car manufacturing.
Skills Required to Work with Robotics in Manufacturing
The integration of robotics into car manufacturing has revolutionized the industry, optimizing processes and enhancing productivity. However, the effective engagement with robotic systems necessitates a diverse skill set, comprising both technical and soft skills. Technical skills are crucial for operating and programming robotic systems. Potential workers should be proficient in programming languages specific to robotics, such as Python or C++, which enable them to interact with and customize automated systems. Moreover, knowledge of robotic operating systems (ROS) and understanding of simulation tools are essential for developing and testing robotic applications. Familiarity with electrical and mechanical systems is also vital, as it helps in troubleshooting and maintaining robotic machinery.
Beyond technical proficiency, workers must also possess strong problem-solving skills. The dynamic nature of manufacturing environments often presents unexpected challenges that require quick and effective solutions. A critical thinker who can analyze a situation, identify potential issues, and implement corrective actions will thrive in such settings. Additionally, workers should be adept at working collaboratively within a team. Communication skills are paramount, as they facilitate effective interaction with colleagues from various disciplines, including engineers, designers, and quality assurance personnel. The ability to convey technical information in an understandable manner is invaluable, especially when addressing non-technical stakeholders.
As robotics continues to evolve, adaptability is a skill that can enhance a worker’s effectiveness in car manufacturing. Being open to learning new technologies and methodologies is essential, as the field regularly adopts innovative practices and solutions. For prospective workers, developing this blend of technical competencies alongside soft skills will better prepare them for a successful career in an increasingly automated automotive manufacturing environment.
Conclusion: The Impact of Robotics on the Future of Car Manufacturing
The integration of robotics into car manufacturing has fundamentally transformed the industry, enhancing production efficiency, precision, and safety. As factories increasingly adopt advanced robotic systems, the benefits of automation become increasingly evident. Robotics not only speeds up the production lines but also reduces the likelihood of human error, thereby improving the overall quality of the vehicles produced. With the advent of technologies such as artificial intelligence and machine learning, robots are now capable of more complex tasks, allowing for greater customization and flexibility in manufacturing processes.
Despite these advancements, several challenges persist. The initial investment required for robotics installation can be substantial, and companies must consider the ongoing costs related to maintenance and training for their workforce. Moreover, the shift towards automation raises concerns about job displacement among assembly line workers, prompting discussions on the need for retraining programs and the development of new skill sets. Balancing the economic advantages of robotics with the societal impacts remains a critical hurdle for the industry.
Looking ahead, the potential for innovation in car manufacturing through robotics is immense. New developments, such as collaborative robots (cobots) that work alongside humans, could foster a more integrated approach to production. Furthermore, advancements in robot technology, combined with other emerging fields like electric vehicles and sustainability, indicate a paradigm shift in how vehicles are designed, produced, and delivered to consumers. As the automotive landscape continues to evolve, it is clear that robotics will play an integral role in shaping the future of car manufacturing, making it a field to watch in the coming years.